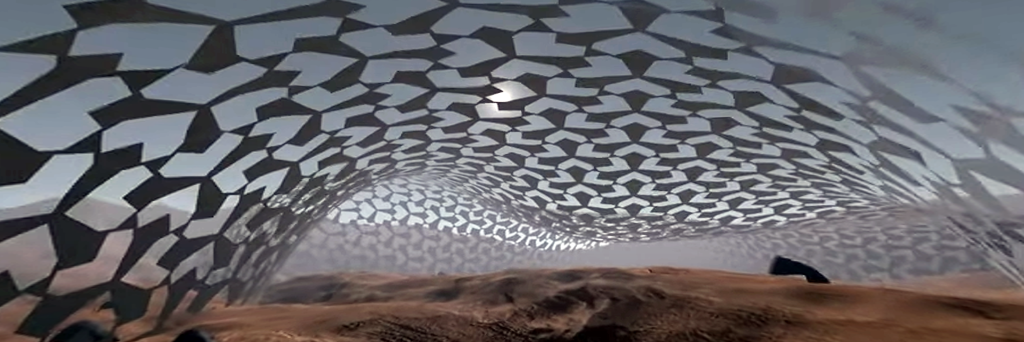
The NASA MIRO Inflatable Deployable Environments and Adaptive Space Systems (IDEAS2) Center at UH was established in 2024 to support the space agency’s strategic goal of extending human presence on the moon and Mars for sustainable, long-term space exploration, development and utilization. The $5M grant is funded by the NASA Office of STEM Engagement Minority University Research and Education Project (MUREP) Institutional Research Opportunity (MIRO) program.
The AIM Lab contributes to this collaborative effort by proposing viable concepts for structures that can be deployed on another planet. We focus our research on three stages necessary to accomplish this mission. One, we generates fabrication, assembly and stowage blueprints to be executed on Earth. Two, we investigate simple deployment mechanisms to transform the stowed structure to its deployed geometry. Three, we analyze the structural and functional performance of the structure once deployed.
The technologies we aim to develop are the following: 1) Geometric frustration based shape generation and deployment, 2) Virtual Reality assisted design and visualization, and 3) CNC based fabrication and robotic assembly.
1 – Geometric frustration-based shape generation and deployment
The goal is this technology is to allow users to specify a target 3D geometry, and design a 2D shape that precisely deploy to that 3D geometry. This problem is first tackled from a differential geometry perspective where, for the moment, mechanics is neglected.
We use the intuition that distortions are inevitable when cartographers map the globe to a flat surface, courtesy of Gauss’s Theorema Egregium. Conversely, by controlling the distortions of a flat surface, we may be able to morph it back into a sphere. Using this fact, we interpret the shape morphing of a surface as a change in its intrinsic curvature. Further, we seek to control the curvature of the surface by affecting a series of coordinated local extensions and contractions.
Local changes to the metric tensor (how distances and angles are measured on a surface) will change the intrinsic curvature of that surface. Specifically, in 2D manifolds, local rescalings of the metric (conformal transformations) can change the Gaussian curvature of that surface. For example, a circular disk will morph to a hemisphere if the center of the disk expands in-plane isotropically by an areal factor of 4, and the edge does not expand.
Fortunately, there exists many mechanical and material systems that can deform isotropically up to prescribed stretches [1]. In this project, we investigate a specific family of unit cells that exhibit isotropy and bistability [2], see figure below.
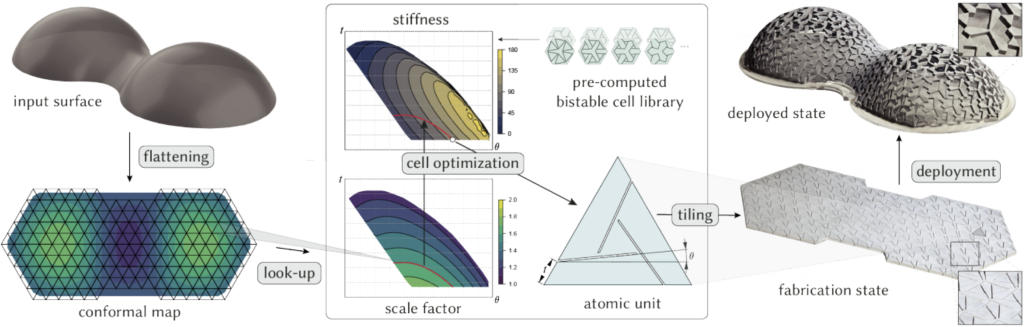
This generative pipeline is being implemented in Rhino+Grasshopper to broaden adoption. Next, we will generate the CNC tool path for each individual unit cell, and use a robotic arm and VR to assist with structural assembly.
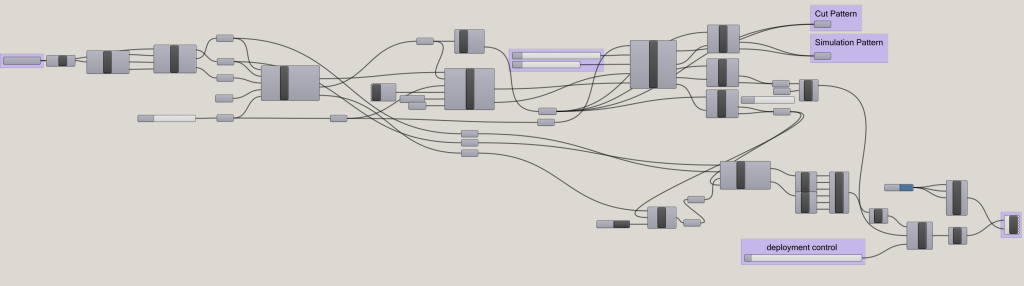
- Wang, Y., Ren, Y., & Chen, T. (2022). “From kirigami to hydrogels: a tutorial on designing conformally transformable surfaces” Journal of Applied Mechanics, 90(4), 044801.
- Chen, T., Panetta, J., Schnaubelt, M., & Pauly, M. (2021). Bistable auxetic surface structures. ACM Transactions on Graphics (TOG), 40(4), 1-9.
2 – Virtual Reality assisted design and visualization
3 – CNC based fabrication and robotic assembly
An AR assembly procedure will be developed. Since each unit cell is geometrically distinct, each will be labeled and tagged using a QR code that is milled on to the unit cell. The AR visualization overlay will then direct the user to place each panel in the correct position to be assembled.